Miglioramento statico degli edifici in muratura. Le iniezioni di malta
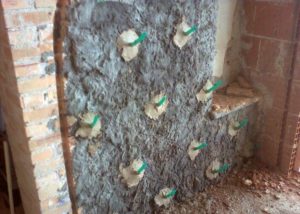
Sempre più spesso ci troviamo ad intraprendere operazioni per la riabilitazione strutturale del patrimonio edilizio esistente, sia per motivi di vetustà, che per la vulnerabilità sismica, costituito nella maggior parte dei casi da muratura. Sono molte le tecniche da conoscere per gli edifici di questo tipo e la “scienza ingegneristica” riconosce dei provvedimenti tecnici d’intervento di riabilitazione, miglioramento e adeguamento, come stabiliti dalla normativa delle Nuove Tecniche di Costruzione del 2008.
Gli interventi localizzati sono sconsigliati come l’unico modo di rafforzamento delle murature se non inseriti in un sistema di riabilitazione dell’intera struttura. In molti tipi di intervento scaturiscono dubbi operativi, che trovano risoluzione anche nell’esperienza degli addetti ai lavori, ma è indispensabile applicare un comportamento di base che induca ad eliminare o consolidare gli indebolimenti locali delle pareti murarie in prossimità degli innesti e degli incroci per l’eventuale presenza delle canne fumarie o vuoti di qualsiasi natura o genere.
Per il consolidamento della muratura, molte volte è necessario inserire nel piano operativo quello che prevede le “iniezioni di malta”
Questa tecnica è applicata di solito nelle murature in pietra, dotate di percentuali elevate di vuoti interni. Questo tipo di tecnica è definita “passiva”, perché non richiede l’esecuzione di operazioni che alterano l’equilibrio o l’aspetto esteriore della struttura e necessita dell’esistenza di vuoti che permettano di far entrare all’interno della muratura le miscele leganti, che hanno il compito di migliorare le prestazioni meccaniche del muro, eliminando le fessure e le cavità, rafforzando così i legami fra i componenti della muratura stessa. E’ un intervento molto diffuso negli edifici del passato, anche di particolare pregio artistico e architettonico, dove si vuole mantenere la struttura il più possibile fedele all’aspetto originario.
PROCEDURA
Si procede facendo penetrare la miscela legante, in pressione o tramite colata nei vuoti presenti attraverso dei boccagli, così da ripristinare e migliorare le caratteristiche meccaniche per la più efficace ripartizione degli sforzi agenti, originata dall’eliminazione dei vuoti stessi. Le miscele sono costituite da acqua e leganti inorganici come la calce o il cemento o da miscele organiche come le resine ed hanno un diverso grado di compatibilità con la struttura originaria, influendo sulla rigidezza e la resistenza dell’involucro edilizio. La tecnologia offre una vasta gamma di materiali per questa operazione ed ognuno di questi ha caratteristiche individuali di cui si deve tenere conto nella fase di progettazione. Caratteristiche fondamentali ed imprescindibili sono l’essere anti ritiro (o meglio a ritiro compensato) e garantire una compatibilità chimico-fisico-meccanica con la malta e gli inerti che devono consolidare.
Per le iniezioni di malte a pressione necessitano le seguenti operazioni:
- Predisposizione di puntellamenti nel caso di dissesti per fenomeni di schiacciamento o pressoflessione;
- Eventuale eliminazione dell’intonaco con messa a nudo della tessitura muraria, senza ricorrere a strumenti a percussione;
- Scelta dei punti per le iniezioni in numero di 2÷4 al mq, da disporre in funzione della tipologia muraria;
- Scarnitura dei giunti per una profondità di almeno 2÷3 volte il loro spessore e spruzzo di acqua e aria in pressione;
- Sigillatura dei giunti murari e delle zone degradate o fessurate per mezzo di malta a base di cemento e sabbia a grana grossa;
- Lavaggio con straccio bagnato delle superfici trattate prima che la malta nei giunti abbia fatto presa;
- Introduzione di eventuali tiranti di acciaio trasversali per assorbire le pressioni d’iniezione;
- Realizzazione di fori di diametro tra i 2÷6 cm (pietrame) e 1 cm (mattoni pieni), attraversanti l’intero spessore murario e, comunque, di lunghezza non inferiore ai 2/3 di tale spessore;
- Cementazione di un’estremità del foro se esso è passante;
- Inserimento di un boccaglio di diametro ¾ di pollice, infisso per una profondità di almeno 10÷15 cm e sigillato con malta di cemento.
La pressione di immissione è fondamentale per evitare il costituirsi delle dilatazioni trasversali prodotte dalla miscela in pressione.
Per le iniezioni di malta per colo occorre procedere con le seguenti fasi operative:
- Eventuale eliminazione dell’intonaco con messa a nudo della tessitura muraria;
- Realizzazione del foro d’ingresso nella zona del paramento in cui la muratura appare più diradata, allargando le cavità già esistenti, ma senza colpi;
- Stuccatura dei giunti, delle cavità e delle lesioni dalle quali la miscela potrebbe fuoriuscire;
- Inserimento nel foro di un ugello, collegato ad un imbuto murato, con malta di cemento a presa rapida;
- Immissione di acqua fino al riempimento completo dei vuoti, segnalato dalla stabilizzazione del livello nell’imbuto;
- Sigillatura delle eventuali lesioni segnalate dalla fuoriuscita di acqua, per mezzo di malta cementizia;
- Immissione della boiacca di cemento (rapporto acqua/cemento compreso tra 1 e 1.5).
Per ottenere buoni incrementi di resistenza tale fase andrà ripetuta dopo 24 e 48 ore, a meno che i vuoti creatisi nella presa non siano limitati con l’aggiunta di sostanze espansive.
Le iniezioni necessitano inoltre di particolari controlli e precisamente:
- Verifica preliminare dell’assenza di fenomeni di schiacciamento o di cedimenti differenziali delle strutture di fondazione;
- Valutazione dell’incidenza dei vuoti nella muratura. Un’indagine con endoscopio su un numero di sezioni murarie quanto più esteso possibile permette di misurare la percentuale di malta, di inerti e di vuoti.
- Prelievo di carote per condurre prove fisiche, chimiche e meccaniche e per tracciare la curva granulometrica del materiale sciolto;
- Verifica dell’eventuale presenza di solfati nella muratura per ricorrere a miscele leganti da iniettare a essi resistenti.
- Confronto tra i coefficienti di dilatazione termica della muratura e della miscela da iniettare, seguito da prove di gelività;
- Controllo della lunghezza dei fori sul 2÷3% dei fori e comunque su non meno di due fori per parete;
- Controllo dell’umidità sugli intonaci dopo il getto (igrometro);
- Esecuzione di piccoli fori spia o di sfiato (Ø <5mm) per evitare l’applicazione di carichi idraulici eccessivi;
- Controllo dell’assorbimento di malta (valori dell’ordine dei 60÷120 kg di miscela a mc di muratura);
- Verifica per mezzo di percussioni della presenza di distacchi all’interfaccia intonaco-muratura;
- Controllo del suono emesso sotto percussioni con martello dalla muratura trattata dopo qualche giorno dall’iniezione;
- Confronto tra prove ultrasoniche condotte prima e dopo l’intervento: gli incrementi di velocità segnalano una buona efficacia delle iniezioni.
VANTAGGI E SVANTAGGI
L’efficacia di questo tipo di intervento dipende dalla possibilità della miscela iniettata di compenetrare all’interno della muratura in modo da raggiungere e colmare tutti gli interstizi presenti; chiaramente affinchè si raggiunga un risultato ottimale è necessario che il muro presenti una tessitura che abbia una continuità tra i vuoti esistenti e la miscela abbia una idonea fluidità in relazione ai tempi di esecuzione.
Le miscele possono essere migliorate con l’aggiunta di additivi fluidificanti, finalizzati ad ottimizzare le caratteristiche reologiche, fisiche e di durabilità degli impasti.
Gli svantaggi di questa tecnica, sono legati alla disomogeneità di distribuzione della miscela e dalla scarsa aderenza ai materiali presenti nella muratura, che molte volte sono di manchevole qualità; è bene quindi prevedere delle prove in loco per verificare le lesioni, i vuoti e le buone caratteristiche meccaniche degli inerti anche se fratturati.
TIPO DI MISCELE
Le miscele a base di cemento sono quelle più utilizzate nelle iniezioni, quando è richiesta una elevata resistenza meccanica e non ci siano incompatibilità con altri materiali. Di solito si usa il cemento Portland oppure quello pozzolanico o d’alto forno. Un dosaggio eccessivo di acqua può provocare fenomeni di ritiro e bleeding a cui si fa fronte inserendo nella miscela polveri silicee o pozzolaniche. Questo tipo di malte è preferibile non usarle nei restauri e nelle murature antiche.
Le miscele a base di calce si usano, quando non sono richieste elevate resistenze meccaniche o in alternativa a quelle di cemento, quando per esempio sono incompatibili con i materiali della muratura e reagiscono con le silici amorfe, originando aumenti di volume. La calce è usata sotto forma di grassello e permette una buona diffusione nella muratura.
Tra gli svantaggi c’è da considerare, che presenta un elevato ritiro e la possibilità di ristagni d’acqua pericolosi in caso di gelo e disgelo. Queste miscele hanno una buona affinità con le caratteristiche meccaniche e fisiche dei materiali che compongono le vecchie murature, tra cui la resistenza, il modulo elastico e il coefficiente di dilatazione termica.
Le miscele a base di resine possono essere di due tipi, a base di resine organiche, per avere resistenze finali elevate o tempi di presa più rapidi e miscele reoplastiche o espansive per ottenere elevate proprietà antiritiro. Scegliere una o l’altra dipende dal tipo di intervento, ad esempio in un intervento conservativo di un edificio monumentale è consigliabile impiegare i materiali già presenti all’interno delle murature, e dagli aspetti economici, infatti le malte cementizie di solito costano circa 10 volte di più rispetto ad un calcestruzzo, mentre se si scelgono quelle epossidiche si moltiplica il prezzo per 100. Solitamente la miscela più adatta, viene scelta in base alle dimensioni dello stato fessurativo da riparare, prevedendo l’uso di materiali più fluidi, come le resine epossidiche per lesioni variabili fra 0,2÷0,3 cm, prodotti speciali a base di cemento o miscele binarie acqua/cemento/sabbia per lesioni fra 0,4÷0,5 cm e latte di cemento per lesioni più grandi di 0,6÷0,7 cm.
La normativa valuta l’efficacia delle iniezioni con un punteggio variabile tra 1.5 e 2 sia per le caratteristiche di resistenza che per i moduli elastici. È consigliabile verificare sul sito il raggiungimento delle caratteristiche meccaniche di resistenza prefissate in sede di progettazione. Un mezzo efficace e di facile impiego per questa valutazione è mediante ultrasuoni, il cui aumento di velocità dopo l’intervento testimonia la riuscita dell’intervento.